The metal aluminum plate process nodes you want are all here! _ Practice
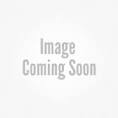
The metal aluminum plate process nodes you want are all here! _ Practice
Original title The metal aluminum plate process nodes you want are all here! Last time in "What is metal aluminum plate" In this article we talked about the basic summary and type analysis of aluminum plates Many small partners left messages saying that they wanted to know about the process nodes and closing of aluminum plates Today we will continue to talk about the use of aluminum veneers mainly to solve the following problems 1 What is the difference between aluminum veneer and stainless steel 2 What is the process node of aluminum veneer 3 What design points should be paid attention to when using aluminum veneer in space 01 Aluminum veneer Expand the full text A disorganized assortment of aluminum panels To be honest like distinguishing the types of aluminum plates it is more troublesome to understand the node practice of aluminum veneers because aluminum veneers are different from "wood" and "stone" which have only a few processes 1 Difference between aluminum veneer custom tailor tape and stainless steel The node practice of aluminum veneer is closely related to the structure shape installation position area size finished surface size and construction period I don't know if you still remember the five most common node practices of stainless steel as shown in the following figure Five Nodal Methods of Metal Veneer The above five methods are abstract expressions for the installation and fixation of almost all metal plates Among them "buckling" (also known as buckling hanging) "gluing" and "nailing" are also applicable to the installation of aluminum veneers 2 Data to be mastered Before introducing the node process of aluminum veneer you need to know some data namely A The maximum conventional specification of aluminum veneers of most domestic manufacturers can reach 6000 mm × 2000 mm For some special sizes the long side can be made to 8000mm (L) × 1800mm (W) B The conventional thickness of aluminum veneer is 25mm 30mm and 40mm For special requirements it can be made thinner (15mm 20mm) or thicker C The most common specifications of aluminum veneer are 600mm × 600mm 600mm × 1200mm and the common width is 1220mm or 1500mm You need to keep in mind the specifications of these aluminum veneers and take them into account in the design of the parting so as not to have the problem of disharmony in the parting as in [wood veneer] boards Wood veneer does not consider design issues due to parting 02 Node Diagram Expression of Aluminum Veneer Next we illustrate the common aluminum plate practices from the shallow to the deep This part mainly explains the installation methods of "gluing" and "nailing" 1 Node practice of adhesive aluminum veneer Adhesive aluminum veneer nodes are the simplest as shown in the following steps Schematic Diagram of Adhesive Aluminum Veneer CAD Node This method is the least difficult in drawing but the most difficult in construction and the most potential quality hazards in the later period Because the larger the area of the metal plate the higher the requirement for flatness the thicker the plate and the easier it is to have a wave effect This gluing method is only applicable to materials with thin plate thickness such as stainless steel plate copper plate etc and the wall thickness is generally 1 bespoken tape measure 2-15mm Schematic Diagram of Adhesive Aluminum Veneer 3D Node When this node method is used for the installation of aluminum veneer it is only recommended to be used for the decoration of small area of wall aluminum plate and it is not recommended to use this method for ceiling and large area decoration Therefore such aluminum veneer method is hardly used in general projects 2 Node practice of nailing-type aluminum veneer Schematic diagram of aluminum veneer As shown in the figure above the installation method of the aluminum veneer determines the factory shape of the aluminum veneer If the "nailing" method is used there will be "small ears" formed by using corner brackets on the aluminum veneer The "small ears" will be fixed with the base steel frame by the "nailing" method and then the gap will be closed by the way of layering or gluing A Node practices are as follows Schematic diagram of elevation installation Cross-sectional node drawing Vertical section node drawing (different nodes for reference) External corner node drawing of nailing method B Site construction drawing Semi-cylindrical aluminum plate This way of nailing and fixing aluminum veneers can almost solve the installation problem of more than 60% of large area aluminum veneers
It is also the most common installation method of aluminum veneer and is widely used in the installation of aluminum veneer ceiling and wall column surface C Example demonstration CAD node drawing Actual construction drawing on site 03 Node practice bespoken tape measure of buckled aluminum veneer We all have a certain understanding of "gluing" and "nailing" Next we will introduce two kinds of "buckle type" aluminum veneer installation methods "dry hanging type" and "buckle type" (These two names are just our names here There is no uniform standard Just remember the node practice) 1 Dry-hanging type A Node analysis Three-dimensional schematic Schematic diagram of elevation Schematic diagram of dry hanging method The "dry-hanging" aluminum veneer node method is typical and its process flow and base layer method can represent all metal plate structures installed by "buckling" and "nailing" The specific construction process is as follows measurement line snapping angle steel fixing vertical keel installation U-shaped groove aluminum installation metal plate cleaning and protection B Key points of design control ① This "dry hanging" method is adopted the spacing of vertical keels is the same as the width of the plate and it is recommended that the width of the metal plate is ≤ 1200mm ② In order to ensure the flatness of the final finishing effect the thickness of the metal plate adopting the "dry hanging" method should not be less than 2 mm The larger the plate is the thicker the plate is and the back rib (reinforcing rib) should be added on the back of the plate to ensure the flatness of the metal plate ③ The spacing of the fixed vertical keel should be ≤ 1200mm but if it is installed on the light block it can not be fixed by this way and it should be fixed on the concrete ring beam or floor slab and structural beam The method of replacing steel frame arrangement with base plate ④ The base plate is used as the base to replace the steel frame to fix the U-shaped groove or nail which is not affected by the size of the plate and is relatively flexible in arrangement However because the base plate is made of wood plywood the fireproof performance is not high ⑤ The internal and external corners of the metal plate of the "dry hanging" method are as follows Schematic diagram of dry hanging node at internal corner Schematic diagram of dry hanging node at external corner 2 Buckle type The node method of buckle-type aluminum veneer is shown in the figure below Buckle type aluminum veneer treatment effect Schematic diagram of the snap-in node Sample of snap-in method Sample of snap-in method This method is relatively simple and crude and it is also a relatively new aluminum veneer fixing method Its advantages are faster installation lower cost and very simple structure than "dry-hanging" aluminum veneer which is widely used in some small space of aluminum wall However in terms of market share it is far less than the "dry hanging" and "nailing" practices so this practice can be understood Brief summary Ok that's all about the process node of aluminum veneer If you have any questions and opinions you can leave a message below Click to save welcome to forward and share Some of the pictures in the article are from pinterest If there is any infringement please contact Xiaobian and return to Sohu to see more Responsible Editor tape-measure.com